Making A Difference
By Gary Buller, Technical Officer, PrintCity
Throughout the pandemic, PrintCity has been exploring how we can best assist in the fight against COVID-19. As a facility which is innovative, disruptive and ahead of the curve, we knew we could make a difference. I thought it would be useful to write about the progress we have made from my point of view as Technical Officer- from the moment we closed the doors through to now, looking into how we adapted to working remotely as a team and the goals we have achieved.
Several PrintCity staff members, myself included took a 3D printer and a small supply of consumables home when we closed our doors. Although relatively safe, these 3D Printers are a different proposition when installed in the home. My house offers little in terms of work surfaces or adequate office space. I have two young daughters, including a curious two-year-old and so I had to place my Ultimaker 3 high on a kitchen worktop, much to the displeasure of my wife.
Safety is essential, especially with children and pets in the vicinity. Using a University template, I completed a new risk assessment for the Ultimaker 3, taking into consideration my children, my wife and its new location. I then sent the same template to other members of the PrintCity team and asked them to do the same. We compiled these in a central location on our PrintCity Sharepoint, and I forwarded them to my line manager, Anthony Gregory, to approve.
With risk assessments in place, I set up a WhatsApp group to quickly exchange knowledge and discuss ideas. We already attended video meetings at least twice a week via Skype, but this was a quicker, more accessible means of communication. The group included Academic Lead, Professor Craig Banks, Senior Lecturer’s Edmund Keefe and Peter Gough, Project Manager Alan Dempsey, Innovation Development Manager (Growth Hub) Mark Chester and Application Engineer Josh Best.
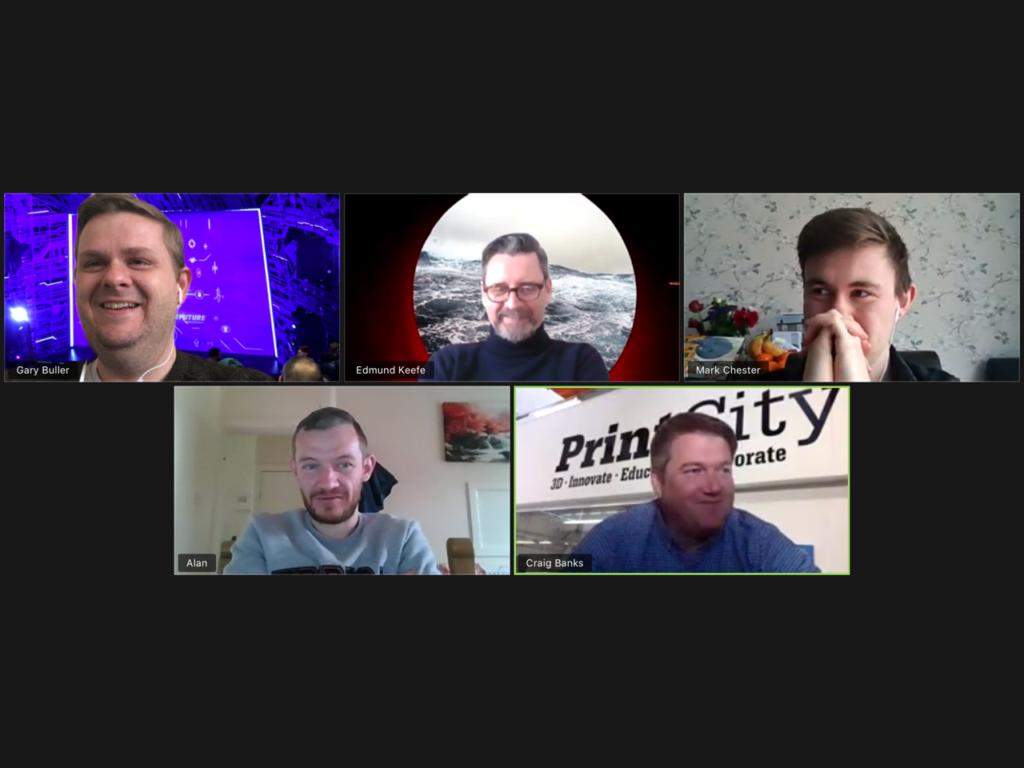
The Venturi Nozzles
The Institute of Engineering and Technology contacted PrintCity with a view to 3D printing some Venturi Nozzles, small but vital components for ventilators. My initial inspection confirmed they were designed for additive manufacturing with no angles below forty-five degrees and the creative use of chamfers to eliminate the need for support, but I also had concerns. A bed of eight or so of these nozzles might take a couple of days to print, and the anisotropic nature of extrusion technology means any air forced through the nozzle could potentially escape between the printed layers, making it difficult to regulate.
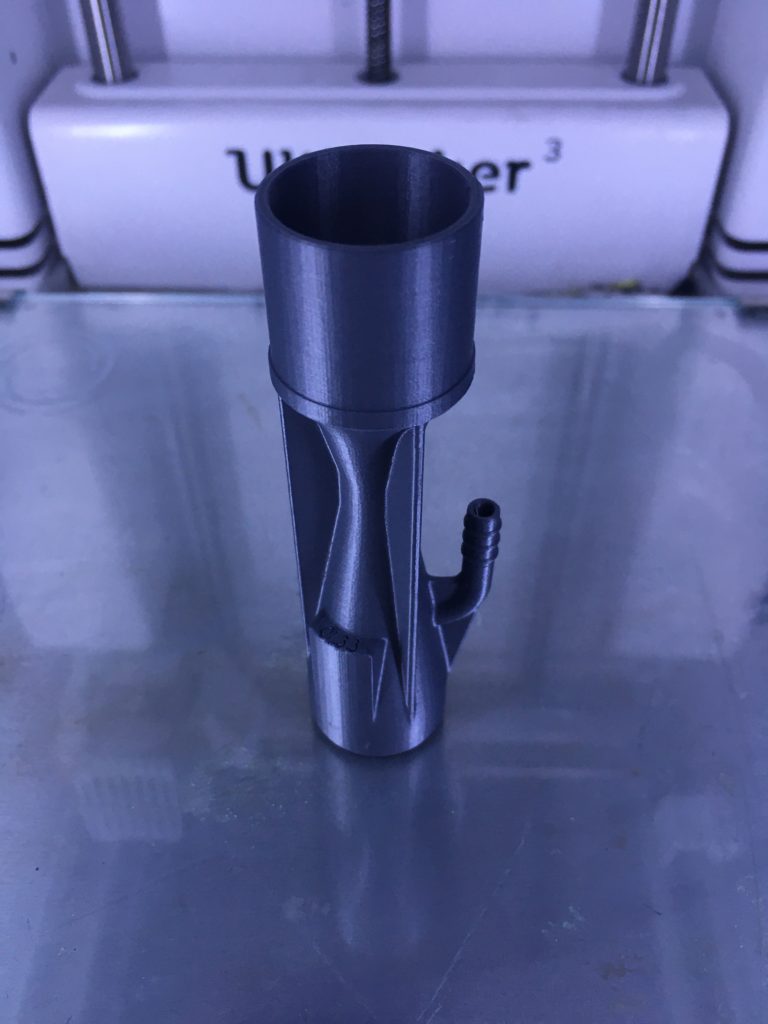
A group of us set about printing prototypes of the Venturi Nozzle. It was during this process I discovered a flaw which made continuation of the project difficult. Inside the nozzle, there was an internal tube which tapered down to a 0.35mm hole. This tube was designed for air to pass through. Extrusion technology struggled to consistently print these holes, even when applying the experimental features and finer resolutions. Blowing the nozzle confirmed little, or no air was passing through it. My colleague, Josh Best, tried the same test with water and came to the same conclusion.
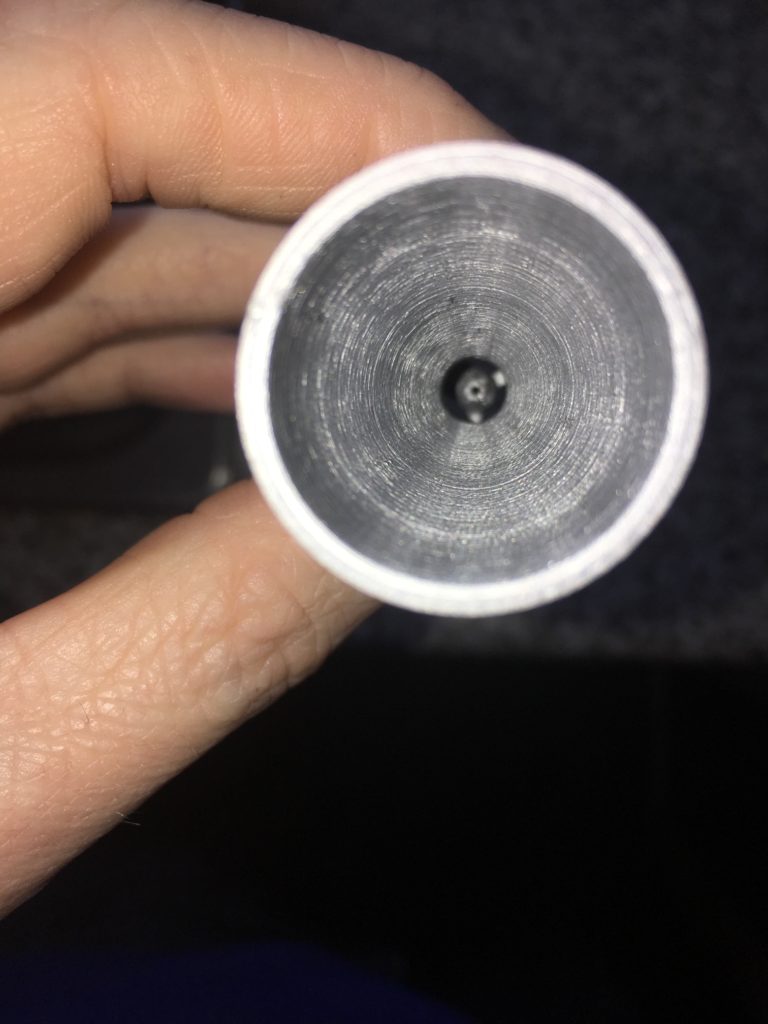
We arranged a Skype meeting with the whole team. We agreed the Venturi nozzle was more suited to multi-jet fusion technology in nylon powder, where finer tolerances and higher quantities can be achieved. Multi-jet fusion is a technology PrintCity will acquire in the foreseeable future, as part of the ERDF funded PrintCity Network bid, but unfortunately not at this time. As a result, it was not feasible to continue testing on the FFF (fused filament fabrication,) CFF (continuous fibre fabrication) and SLA (stereolithography) technologies we had at home. The positive takeaway from the experience was how agile we could work as a team of remote users, and how quickly we could produce and test prototypes.
ARMie
Innovation Development Manager Mark Chester (Growth Hub) was already working on another idea which was very much in line with PrintCity’s innovative and forward-thinking philosophy. Materialise, the Belgian company responsible for file-fixing software, Magics, designed a hands-free door opener which would bolt to a door handle and reduce the contact spread of COVID-19. Mark took this idea, developed an evolved version and presented it to the group. We eventually named this the ARMie. Mark’s blog post on this can be found here.
The group discussed Mark’s idea over Skype, and we made suggestions through the WhatsApp group- sharing and comparing pictures, drawings and prototypes. We thought it would be a useful addition to places housing vulnerable people, like hospitals, nursing homes, nurseries and GP’s surgeries. The design changed from three assembled components to just one. We simplified the part, so it printed quicker and used less material. The shape of the part altered to be more ergonomic. Professor Banks suggested we secure the part using cable ties instead of bolts, which opened the design up to a broader range of door handles and made it easier to install. We decided to make ARMie open source and available at several locations on-line.
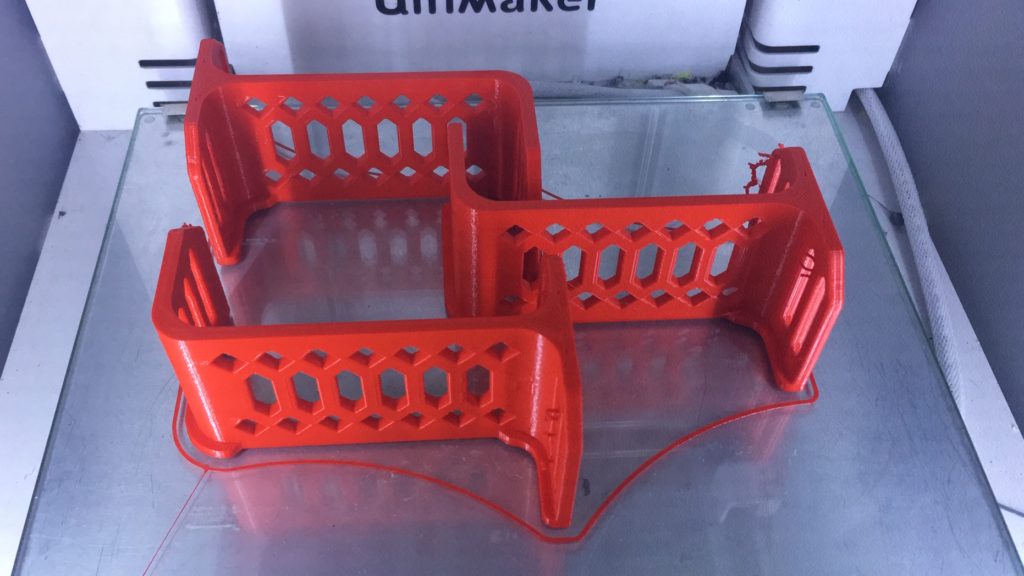
I happened to mention the ARMie to the manager of my daughter’s nursery, and she expressed an interest. I told her it was open source and so the nursery obtained several 3D printed ARMie’s to test in their dining room, utilising them on the handles of cupboards containing food and playthings for the children. Overall, we’ve had a lot of positive feedback and have been made aware of others using the device successfully. The evolution of the ARMie continues, and I have since prototyped the ARMIE in an antimicrobial filament, hoping to take it to the next level.
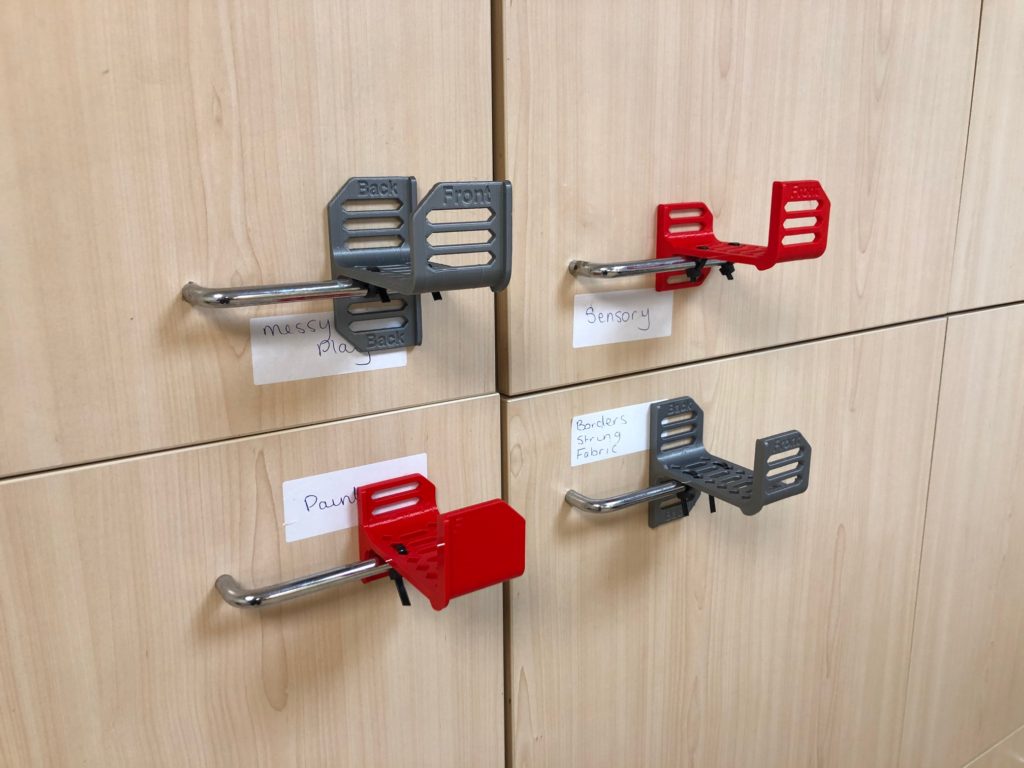
ARMie is an exciting product with applications beyond the COVID-19 pandemic. During our research, we saw other devices with the same purpose, which lacked the additive optimisation and design simplicity. Some of the devices hadn’t been thought through or were impractical. Fusion 360 includes parametric modelling which means we can adapt these designs to different handle profiles. ARMie is something which can be used to protect vulnerable people indefinitely.
3D Printing Curriculum Developer Print Lab together with PrintCiy have since launched a free lesson plan focused on developing COVID-19 solutions. The project will teach students about how the virus is transmitted and encourages them to design products like ARMie which will prevent the spread of infected droplets.
The PPE Visors
During the process with the ARMie we were contacted by the Northern Care Alliance NHS Group to assist in the 3D print of pre-approved visors for Salford Royal and Oldham Hospitals. This was something we were only happy to do. With a larger capacity than other additive manufacturing facilities in the region and our high standard of 3D print expertise, it made sense.
I was involved from the outset, sending a complete list of our printers to the Northern Care Alliance and enquiring what their preference in print materials was. Their initial choice was PETG (Polyethylene Terephthalate Glycol,) but they were happy for us to print in PLA (Polylactic Acid.) PLA is less likely to warp than PETG and is a more reliable print. Moreover, every home hobbyist with a 3D printer and a willingness to help the cause was ordering up PETG and stocks were low.
The visors we printed were a modification of a design created by Prusa, manufacturers of 3D printers. It is a hardy visor which is comfortable to wear and easy to sanitise for reuse. It was a design, cleaning and assembly process which the Salford Royal NHS Foundation Trust’s Clinical Lead had already approved. We modified the file so we could fit an optimum number of prints on our print beds within 24 hours, eight on a standard bed and sixteen on the larger beds.
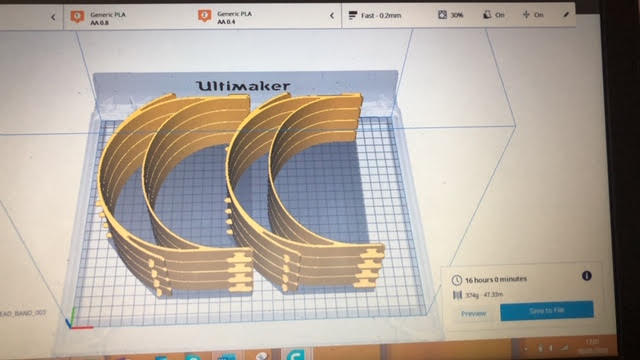
I ordered two weeks’ worth of PLA filament (based on my calculations of consumption) through our applications engineer Josh Best, who’s role is divided between supplier GoPrint3D and PrintCity. The immediate benefit was Josh was able to tell me levels of stock available and backorder where required. He was also able to directly courier the filament to PrintCity during the times we were open.
Of course, this meant getting into the PrintCity building safely to access the printers. Project Manager, Alan Dempsey worked very hard to make this possible. I assisted Alan in writing safe operating procedures and risk assessments with a view to the University’s Health and Safety, Security and Estates teams to give the go-ahead to re-open. Strict control measures had to be followed to ensure the staff were safe and maintained social distancing rules. Letters from University HR confirmed that we were producing visors for the NHS were then distributed, to allow us to travel to and from PrintCity.
Eventually, we returned to PrintCity. Alan compiled a rota of twelve volunteers, and we set to work. A typical shift involved two staff members. We would remove a batch of prints from the machines, clean the bed and then set a new batch printing. The successful prints were post-processed, bagged up and collected weekly by an NHS representative. We managed to produce 1200 hardy, reusable visors in less than a couple of weeks.
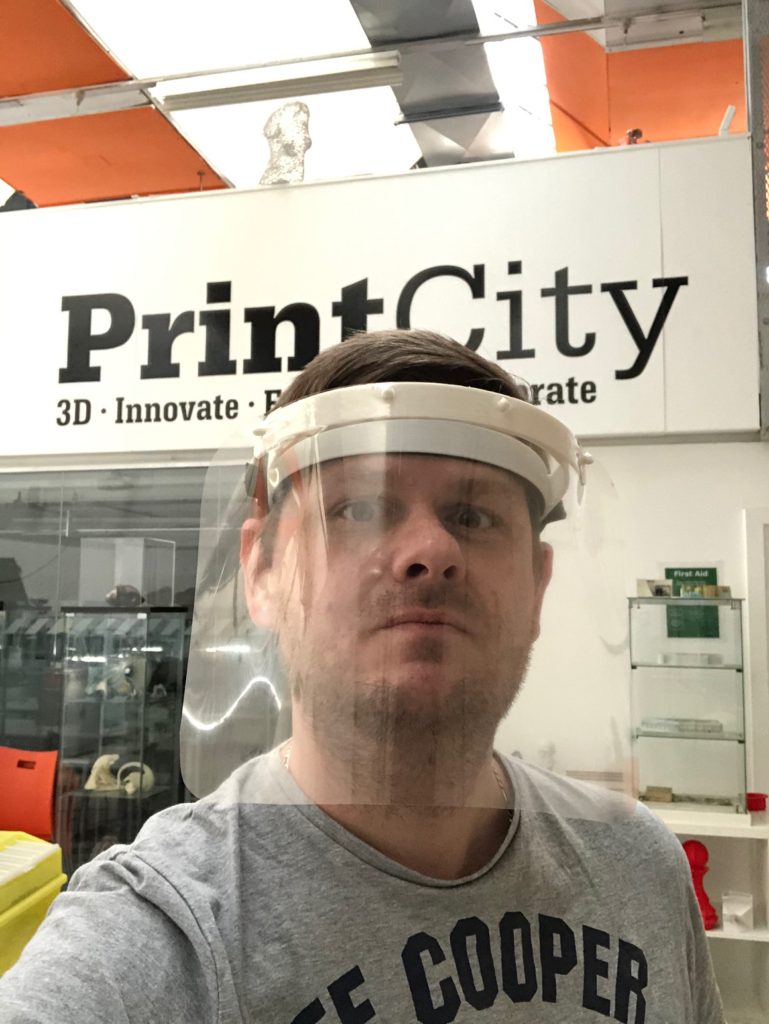
The PPE supply chain was always going to catch up, and the NHS find a quicker, more economical way of producing the same visors, through a combination of their suppliers and injection moulding. On the week of 20th April, the Northern Care Alliance thanked us for our efforts and collected the final batch of visors. It was a significant achievement for all involved, and I am proud to have been part of this.
The Move
Throughout the pandemic, PrintCity has been planning for our imminent move to Turing House. From a Technical Services perspective, this means ensuring we can continue to provide high-quality support for students, academics, research and knowledge exchange.
I have compiled a new presentation, The Principles of Design for Additive Manufacturing, which I aim to deliver in addition to our practical FFF (fused filament fabrication) workshops upon our return. This presentation will focus on mindset when producing designs for additive manufacturing, optimising 3D prints and considerations when working with additive technology. I am also working on an additional presentation on file-fixing in addition to carrying out experiments and research for an academic paper.
Technical Services have been integral to PrintCity’s move to Turing House from the beginning, both myself and our apprentices being involved in decision making around where our technology will go and how the new workspace will look and feel. In preparation for the move, I have allocated our Technical Services apprentices the task of creating standard operating procedures for some of the tasks we undertake, risk assessments to complete and posters to design whilst at home. I have also been working on updating our risk assessments in preparation for the move, though these can’t be fully complete until everything is placed in our new location.
In addition to our move to a new home, the facility is expanding at a rapid rate. PrintCity Network, Transform-CE, Sharepair and Cirmap are all on the horizon. As a Technical Officer, I am valued as a skilled resource and am very much part of the wider team, standing shoulder to shoulder with my academic and non-academic colleagues to achieve a common goal; to innovate, educate and collaborate. This has never been more apparent than during this pandemic where we have come together to achieve results with a rapid turnaround. The limitations of segregation have only served to foster greater creativity, and it has been fantastic to work towards a common goal. I believe the future for the Technical Services team within PrintCity is bright, and I look forward to the challenges ahead.
Get in touch
If you're interested in working with us, or have questions about studying with us please get in contact.

Related Blog Articles

